General
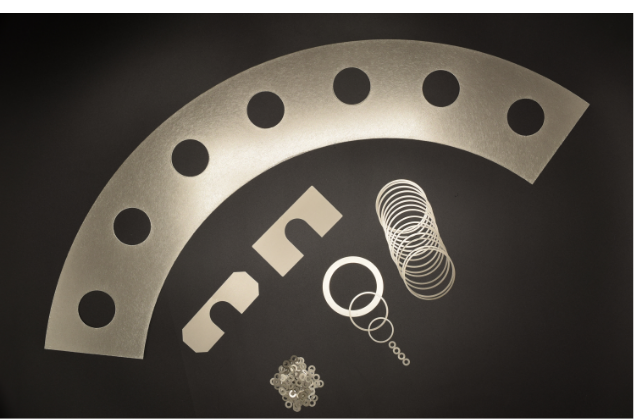
Reducing component size and improving force transmission is an ongoing trend in many industries. The more the coefficient of friction is optimized, the smaller and lighter the design of the two contact parts can be. Increasing the coefficient of friction thus makes a decisive contribution to energy and materials savings in a multitude of industries. From chassis and other vehicle components, to the machine industry, wind power, precision robotics and aerospace applications, you can significantly increase system performance by achieving up to 5 times the static coefficient of friction, while reducing component size by using smaller, lighter bolts and fasteners.
OPERATION
DIANIP friction spacers are thin, precise and elastic metal sheets coated with a fine nickel layer incorporating diamonds. The parts are typically only one tenth of a millimeter thick, weigh less than a gram, and require no change to the system design. The use of a friction spacer reduces the weight and complexity of a mechanical assembly, making it a cost-effective solution.
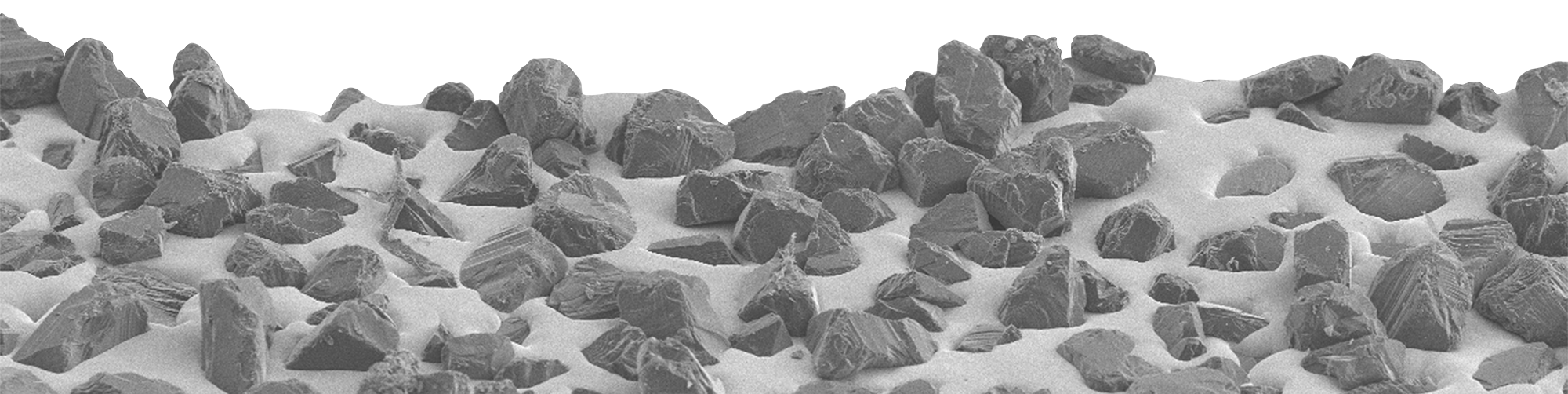
Friction shims applications
Aerospace industry
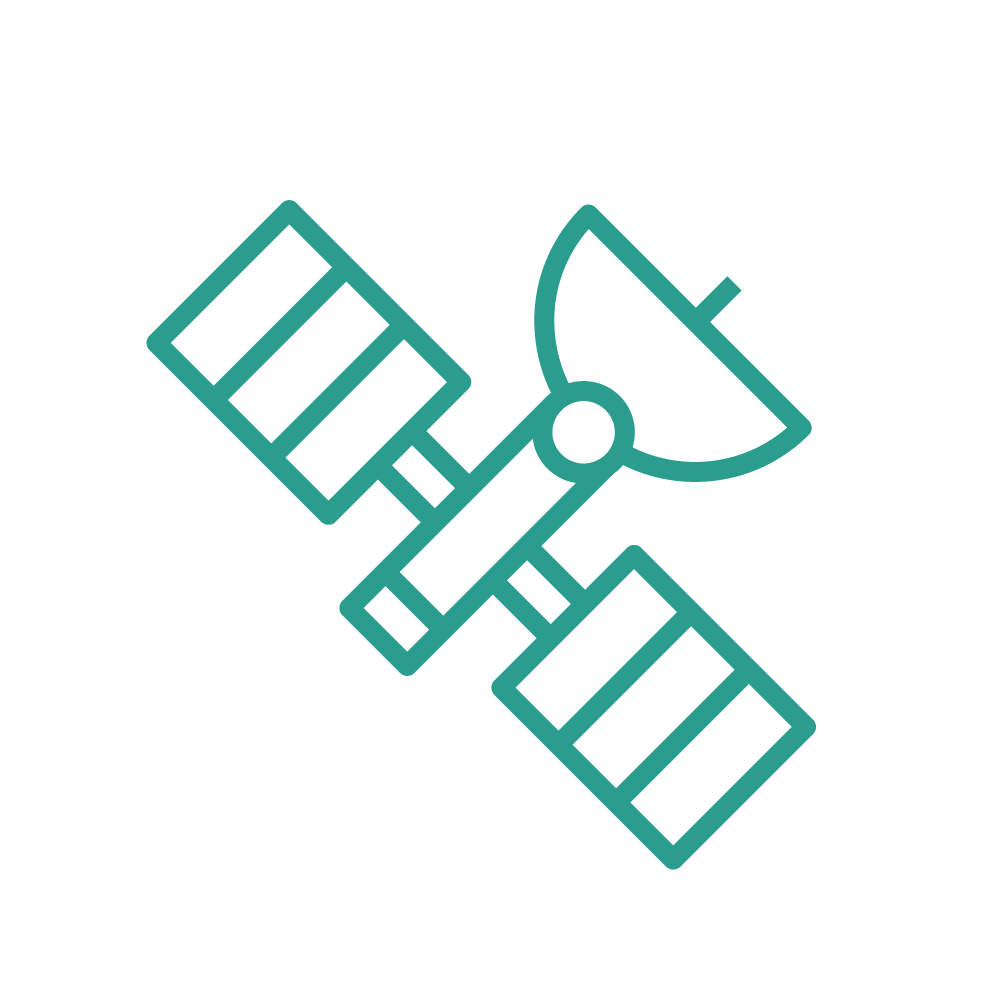
There’s no other area where weight and size reduction is more important than in space applications. For this reason, DIANIP friction shims are the perfect solution for effective size reduction and increased performance.
How does it work?
DIANIP friction spacers are thin, precise and elastic metal sheets coated with a fine nickel layer incorporating diamonds. The parts are typically only one tenth of a millimeter thick, weigh less than a gram, and require no change to the system design. The use of a friction shims reduces the weight and complexity of a mechanical assembly, making it both a reliable and cost-effective solution. From rockets to satellites, DIANIP friction shims are used in a wide range of applications. Capable of withstanding extreme conditions, they protect and reinforce critical system points such as loosening or slipping, reducing the risk of failure.
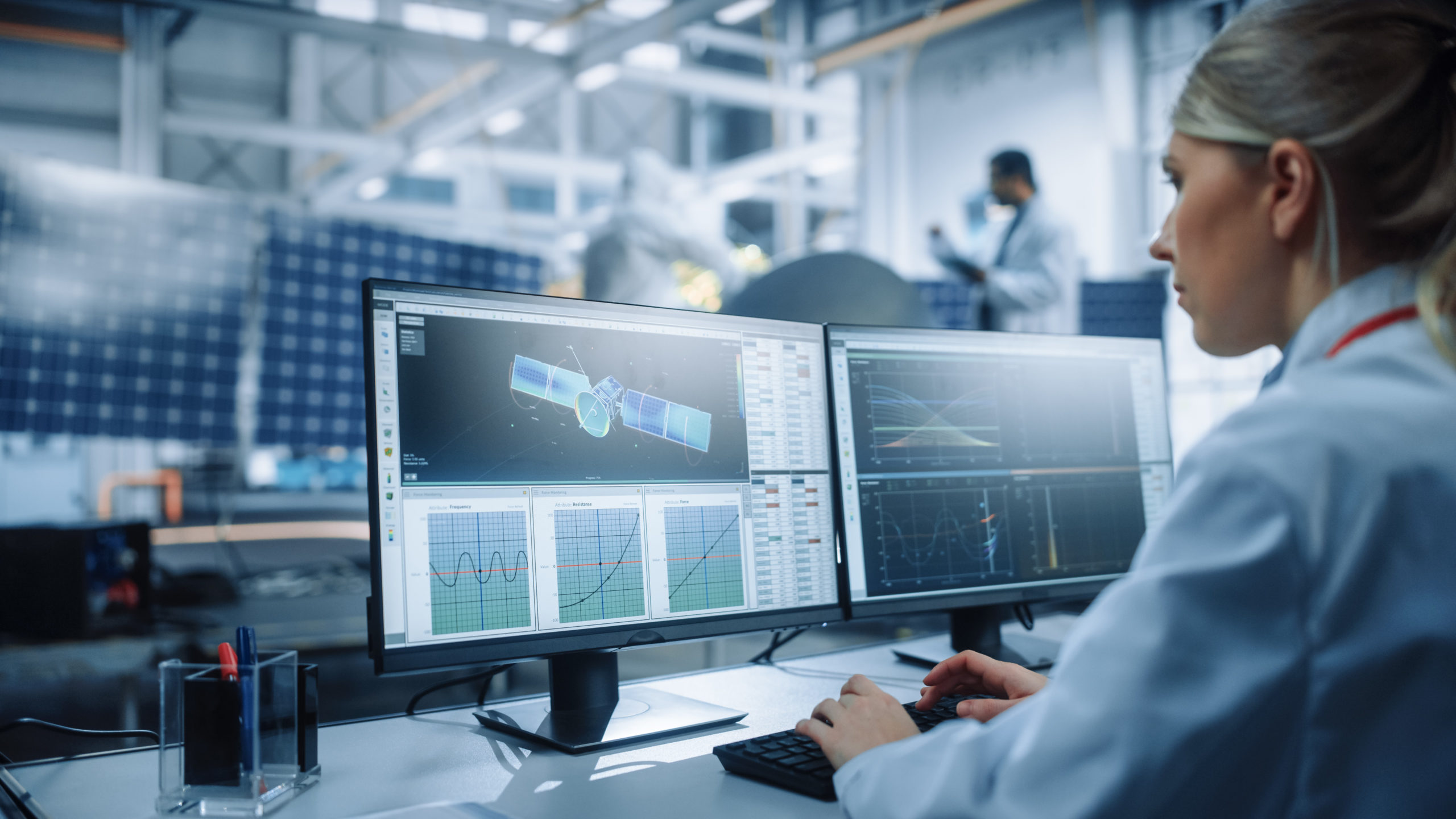
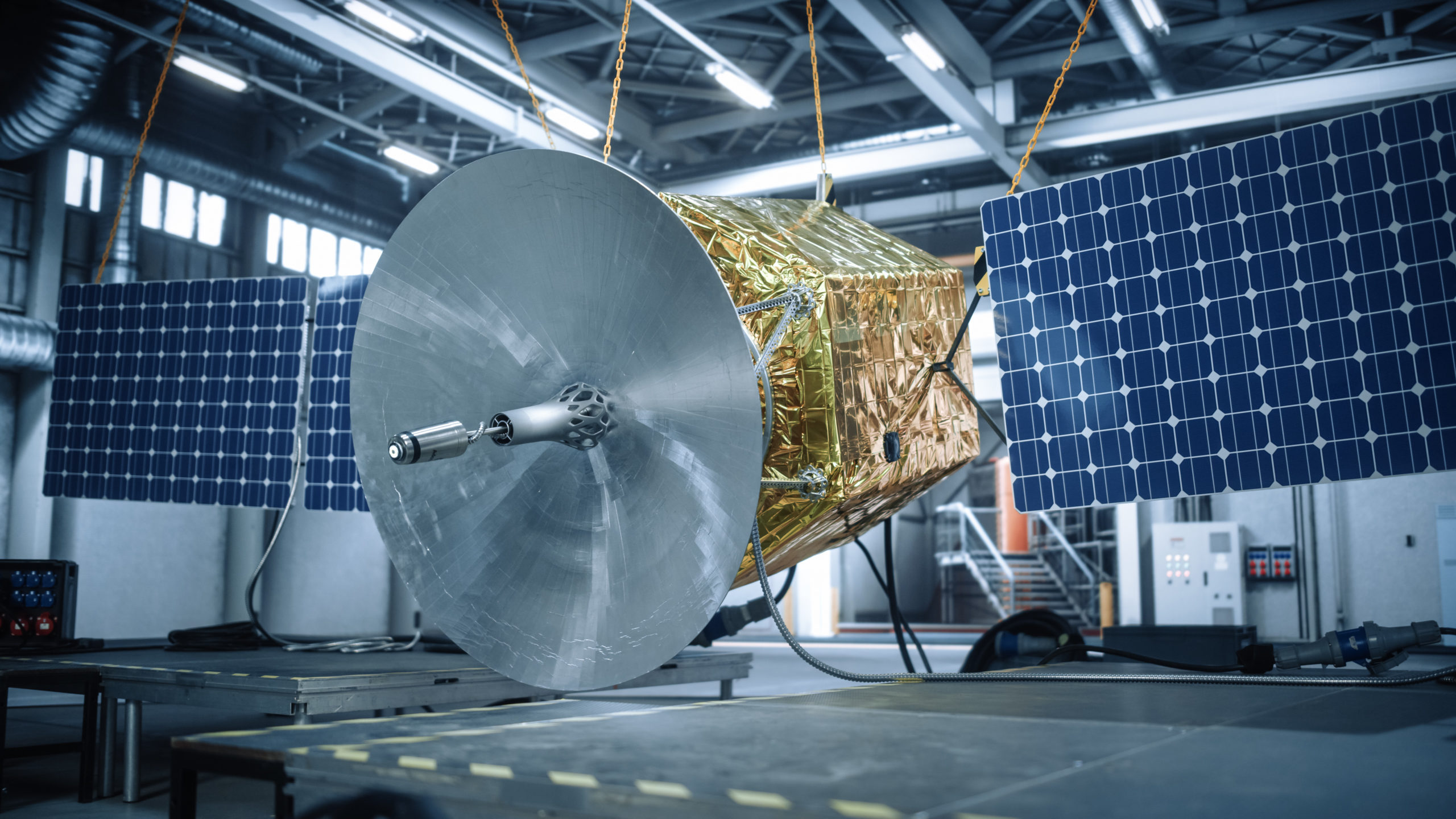
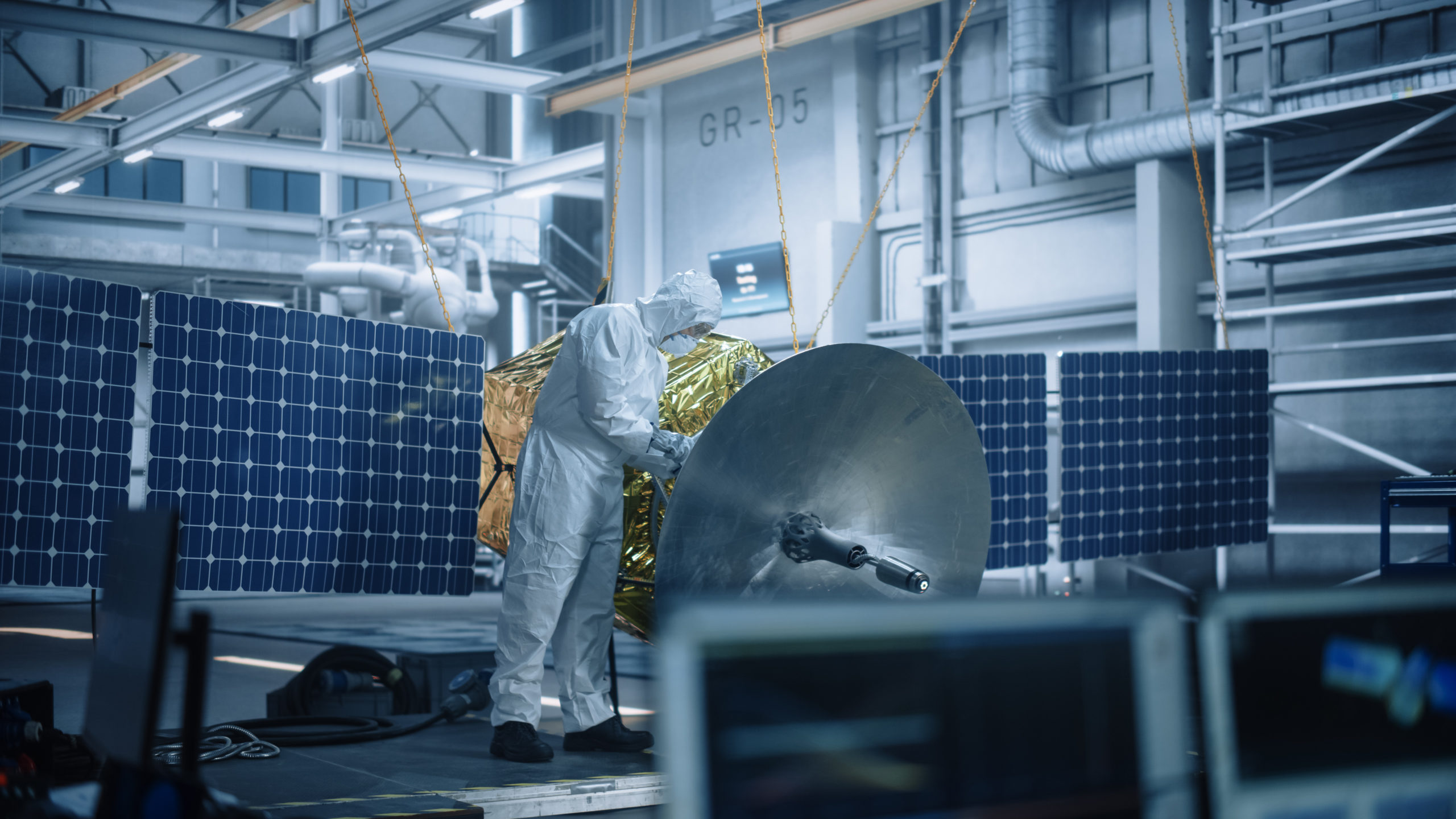
Our DIANIP friction spacers can be used in the very structure of sattelites, as well as on rotating cylinders, robotic arms and space telescope mirrors.
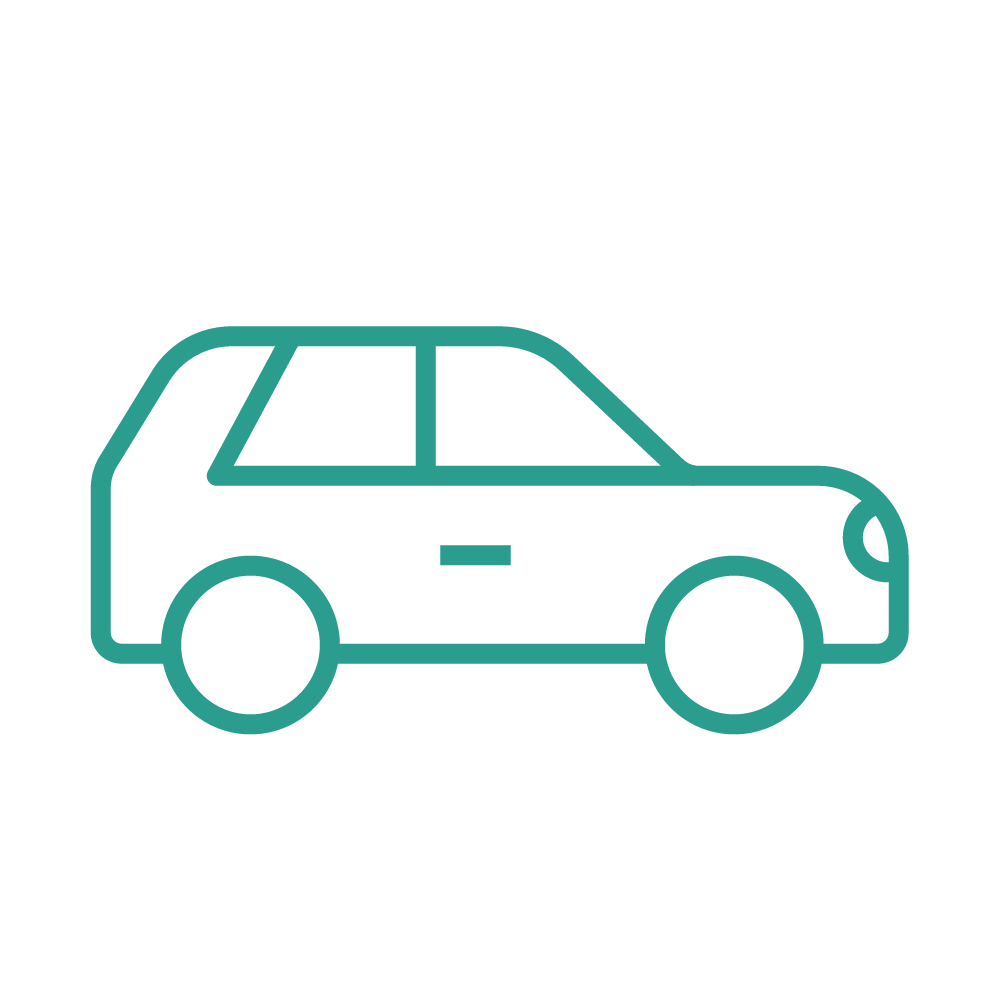
Automotive industry
The automotive industry uses DIANIP friction shims to increase efficiency thanks to the adhesion provided by diamonds, enabling higher torque to be transmitted while protecting the assembly against shear loads in bolted joints.
Miniaturizing engines to reduce fuel or energy consumption, while increasing the coefficient of friction to enhance torque transmission, are the challenges that DIANIP friction shims can meet.
How does it work?
DIANIP friction spacers are also used in the engine, between the crankshaft, pinion and torsional vibration damper, on the camshaft and in connections between gearboxes. They can also be used in the chassis, as suspension brackets or as steering bar brackets on the subframe. In some cases, friction spacers can be used in conjunction with other types of mechanical fasteners, such as bolts or screws, to provide additional stability to reduce or eliminate unwanted movement or play between mechanical components. The aim is to reduce noise and vibrations throughout the vehicle, thus enhancing passenger comfort. With the development of hybrid and electric vehicles, the challenge of reducing weight and size has once again become more pressing, and friction spacers offer a simple, high-performance and cost-effective solution. The rapid development of vehicle electrification and performance demands mounting solutions capable of withstanding ever-greater stresses. DIANIP friction shims increase the strength of fasteners between chassis and batteries. All this while reducing the size and weight of the system, thanks in particular to the miniaturization of the fasteners.
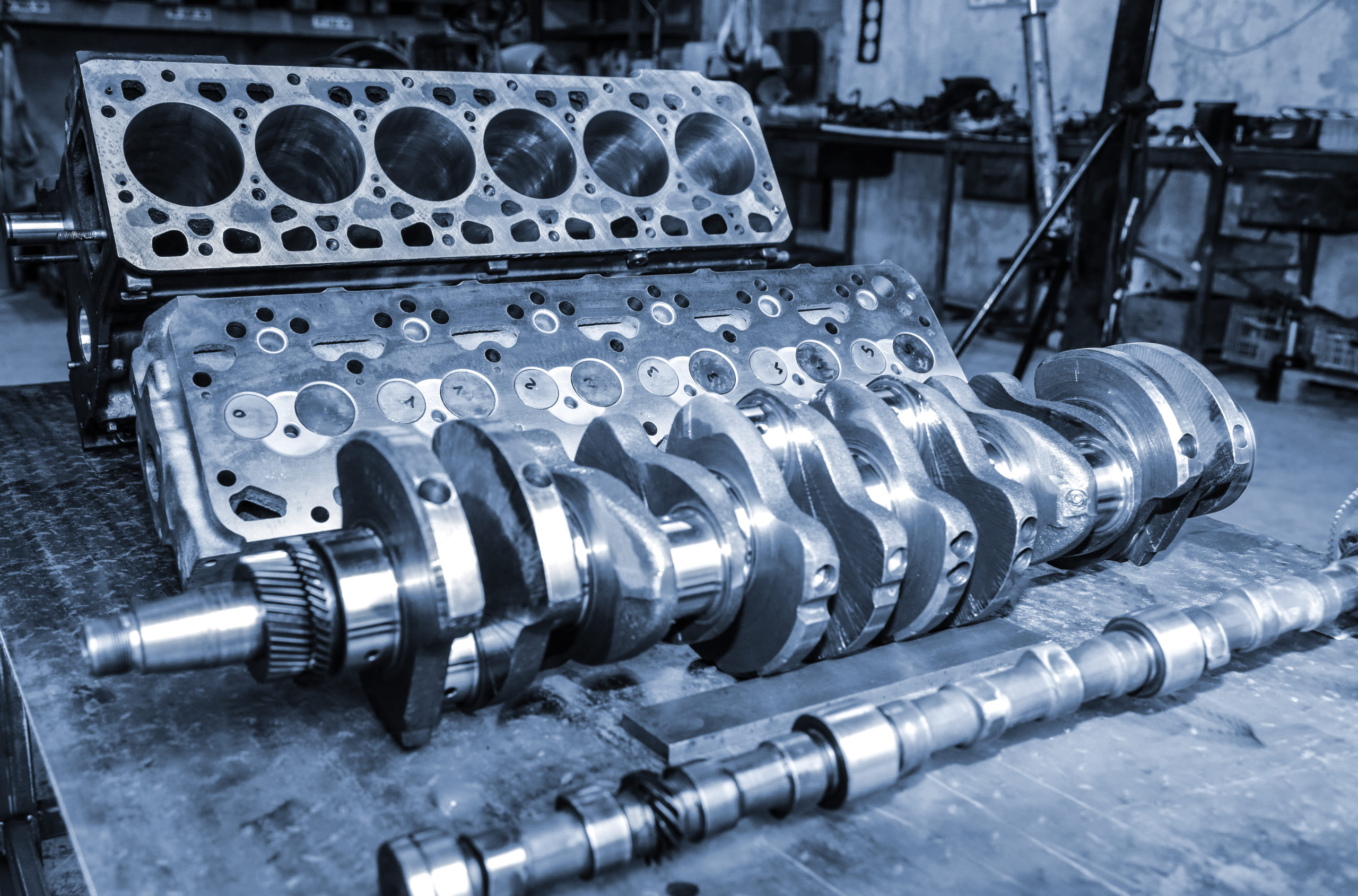
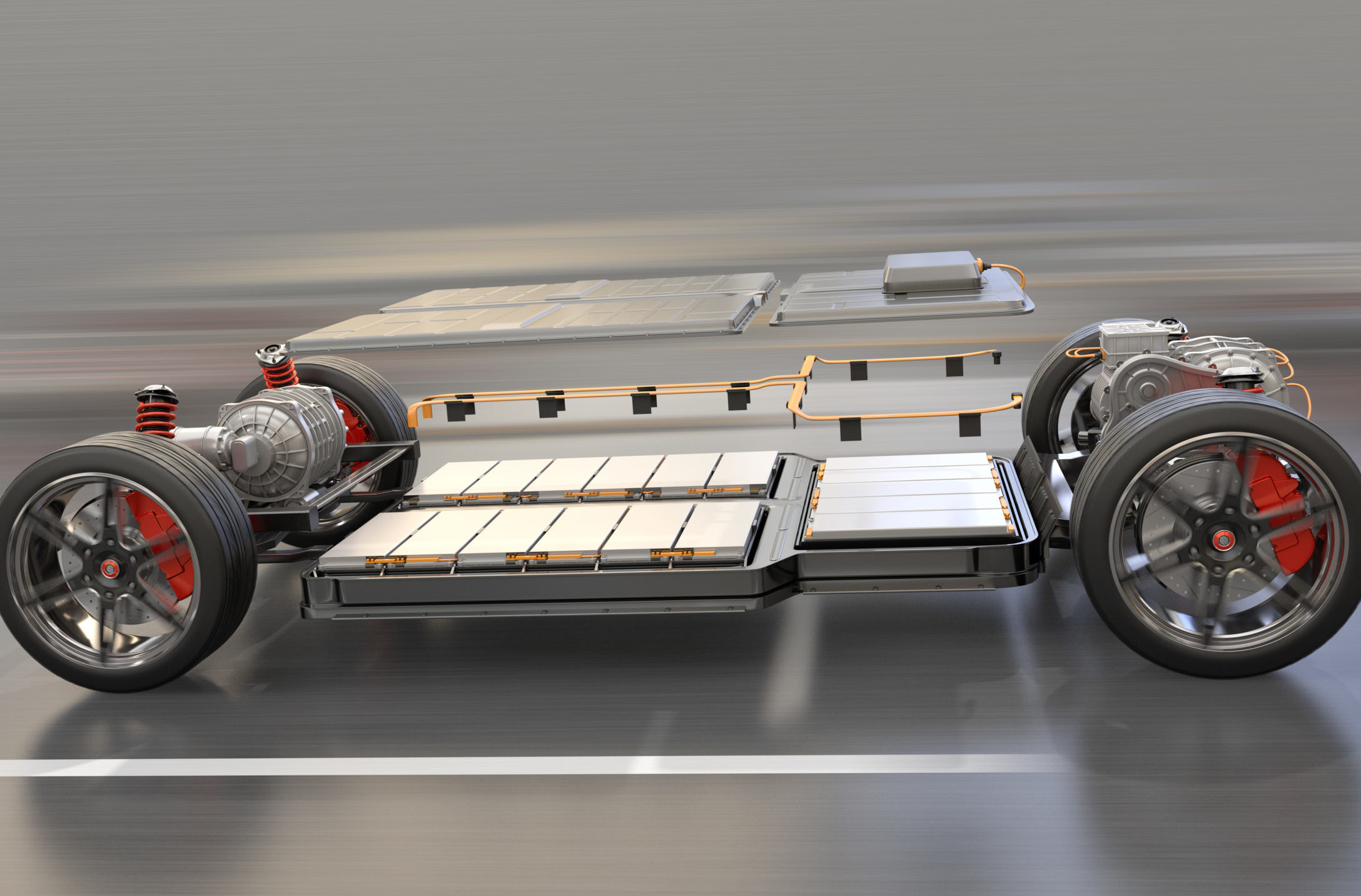
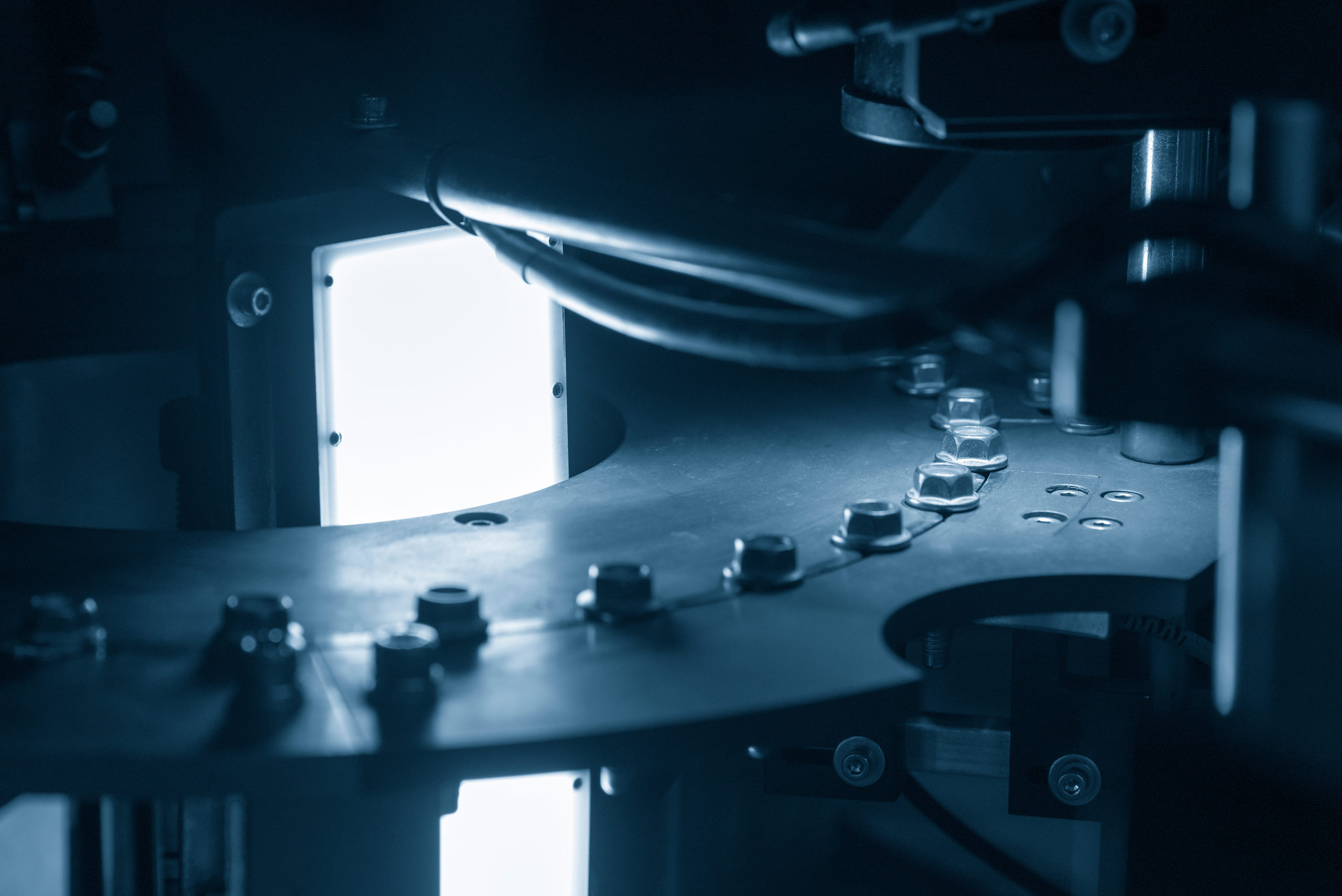
Easily increase statibility and reliability when mounting/assembling electric vehicle batteries without changing the design or adding other mechanical fasteners.
Robotics industry
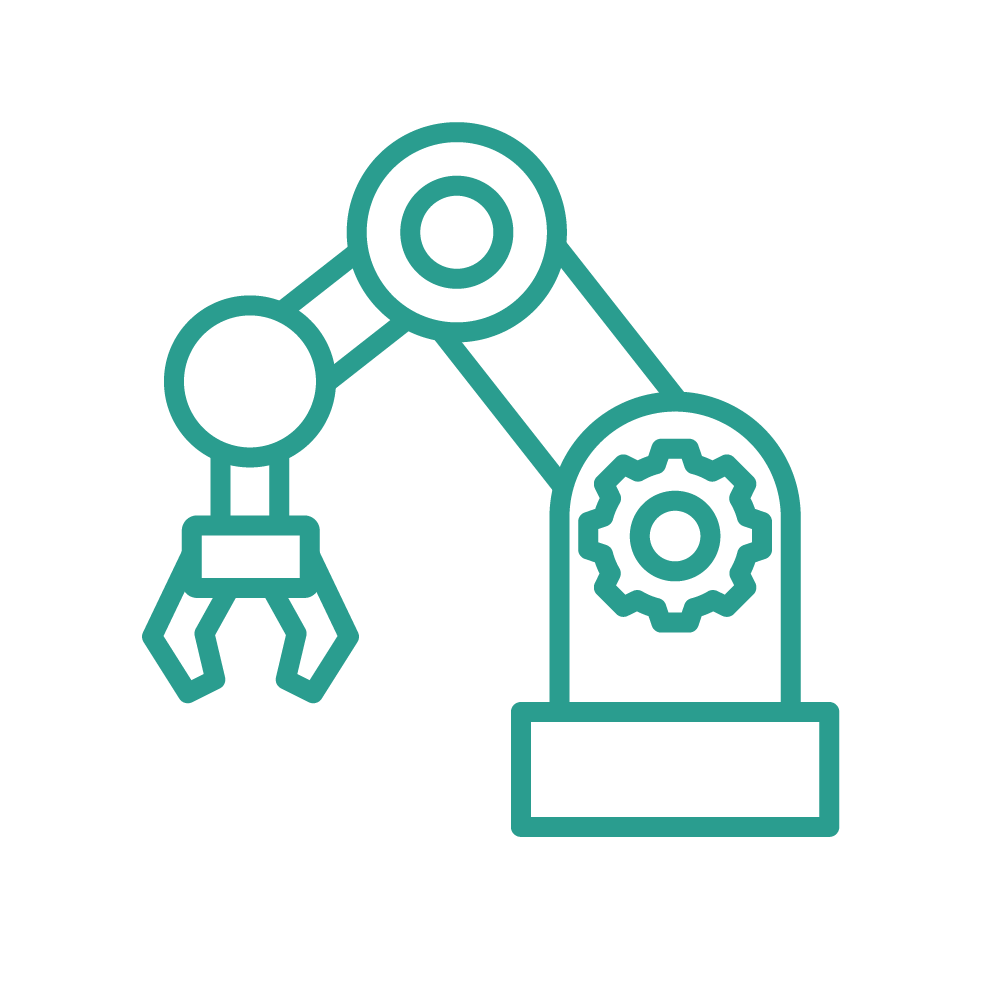
Today, robotics is an increasingly integral part of the industrial world. These robots are focused on precision as well as efficiency, and require reliable solutions to increase performance by reducing vibration while reducing component size.
How does it work?
DIANIP friction spacers are mainly used in robot wrists, end effectors, joints/links and grippers. They are often installed in confined spaces, giving them the advantage of miniaturized components. What’s more, the increased speed, acceleration and vibration to which these robotic arms are subjected make increased friction a key variable in this sector.
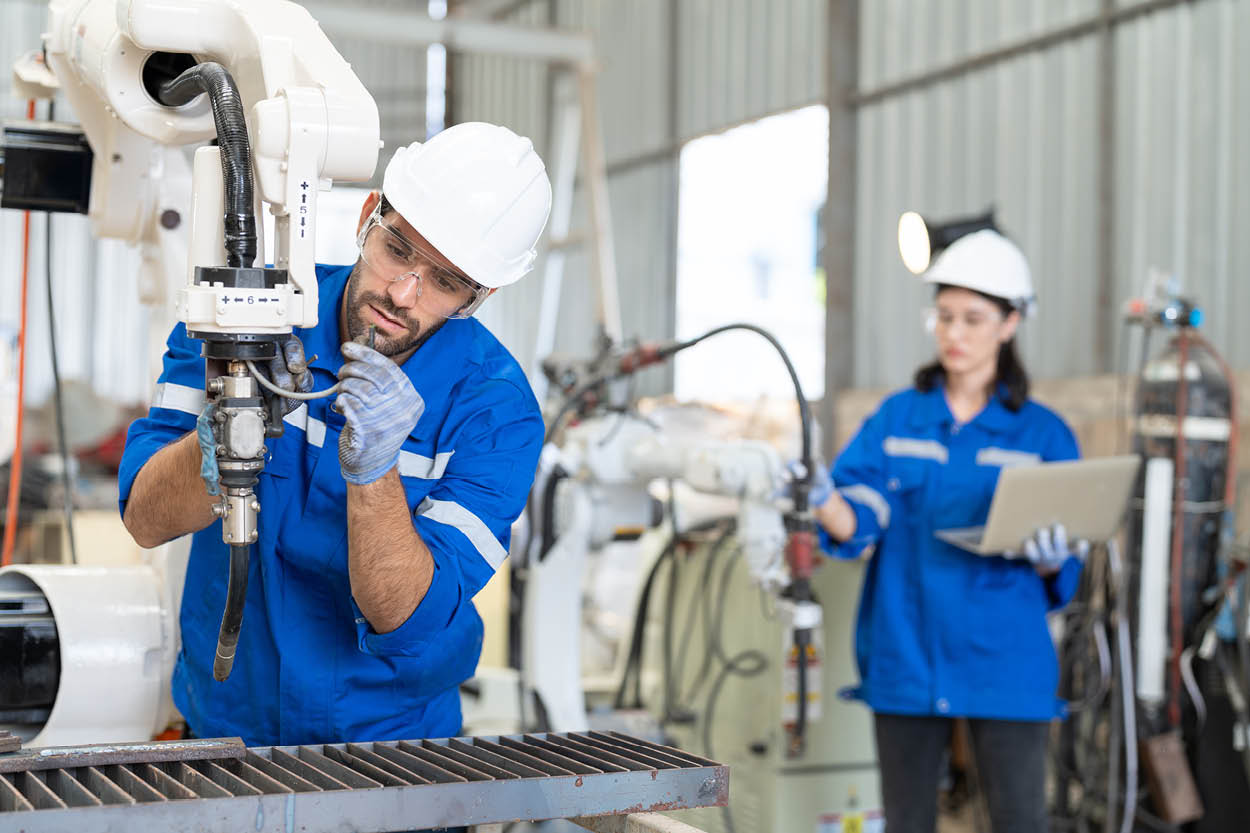
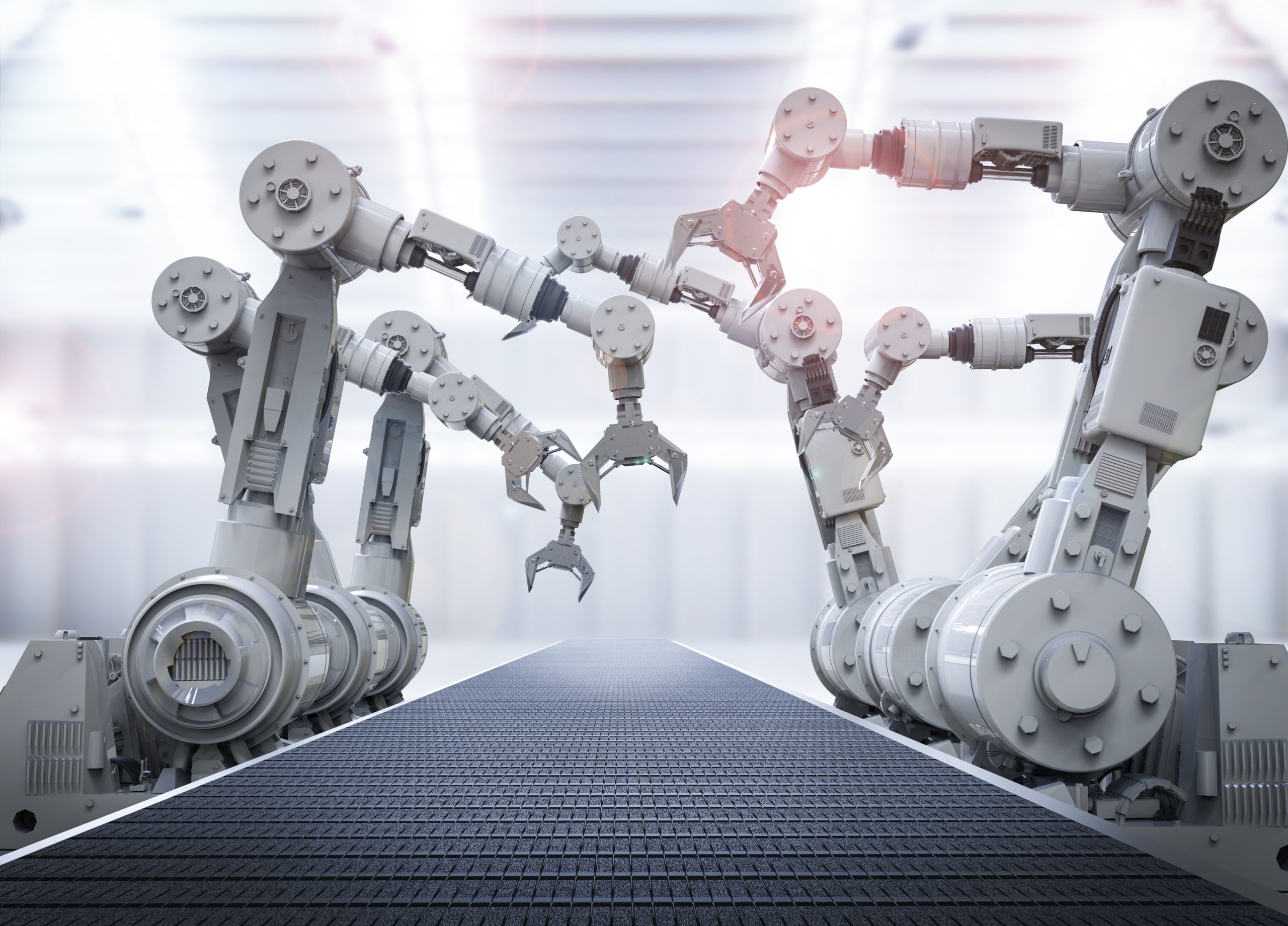
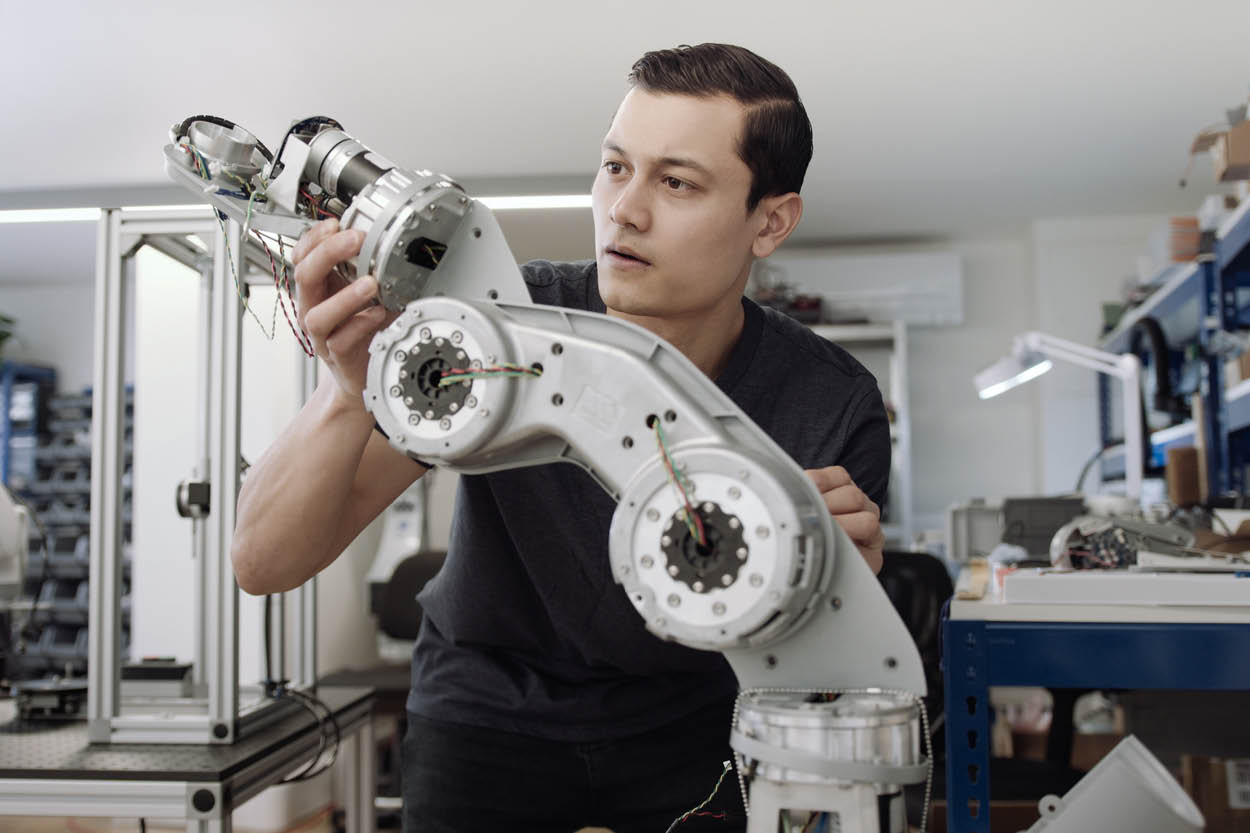
Whether articulated robots on industrial production lines, humanoid robots, cobots or hybrid robots, our friction spacers are used in a wide range of robotic applications.
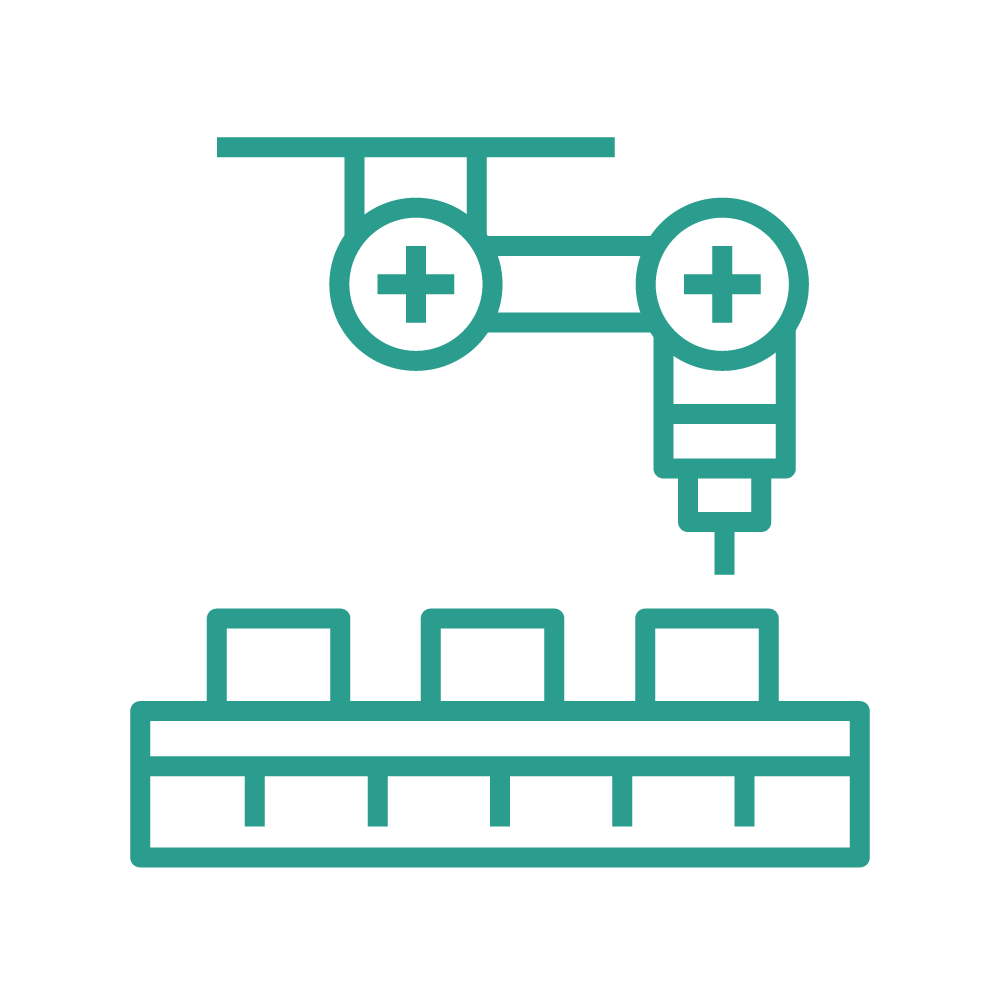
Machinery industry
Increasing the coefficient of friction of a surface can be very useful in certain areas of the machine industry, such as gripping or locking a moving part in a defined position.
How does it work?
DIANIP spacers improve the coefficient of friction, enabling better force transfer. The electroless nickel matrix, in which diamond particles of defined size are embedded, enables high surface roughness to be achieved in order to transmit high force torques without damaging the driven part.
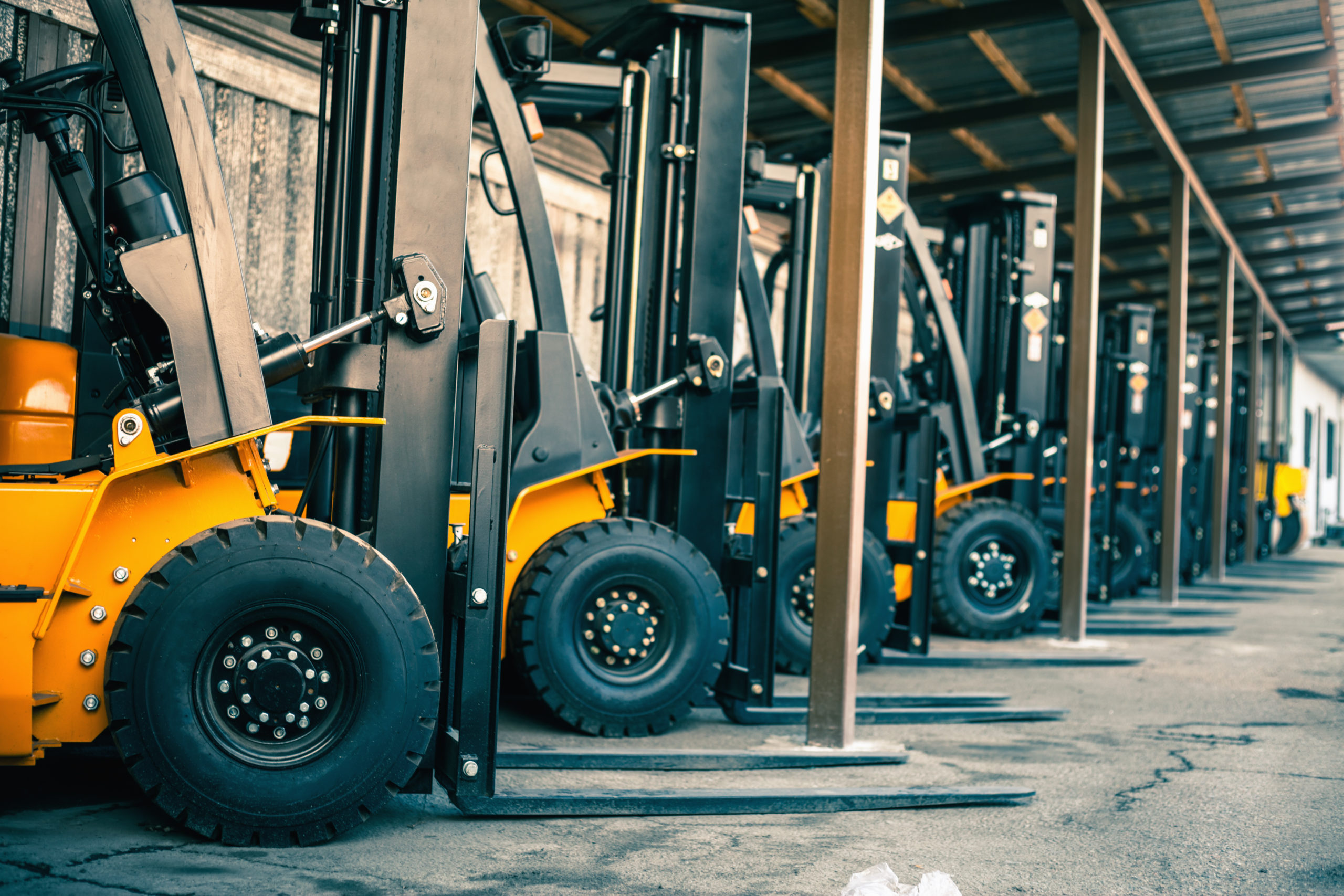
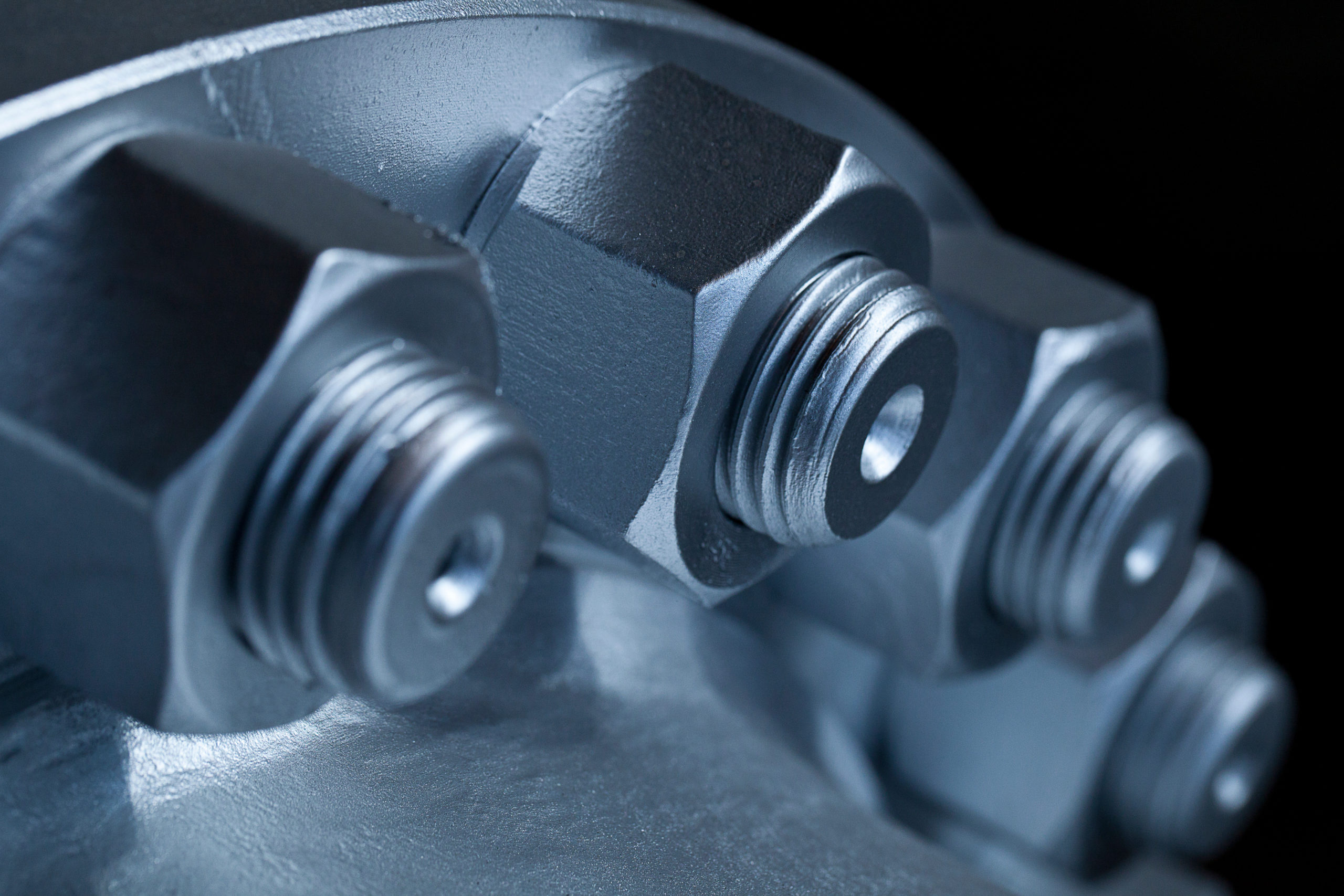
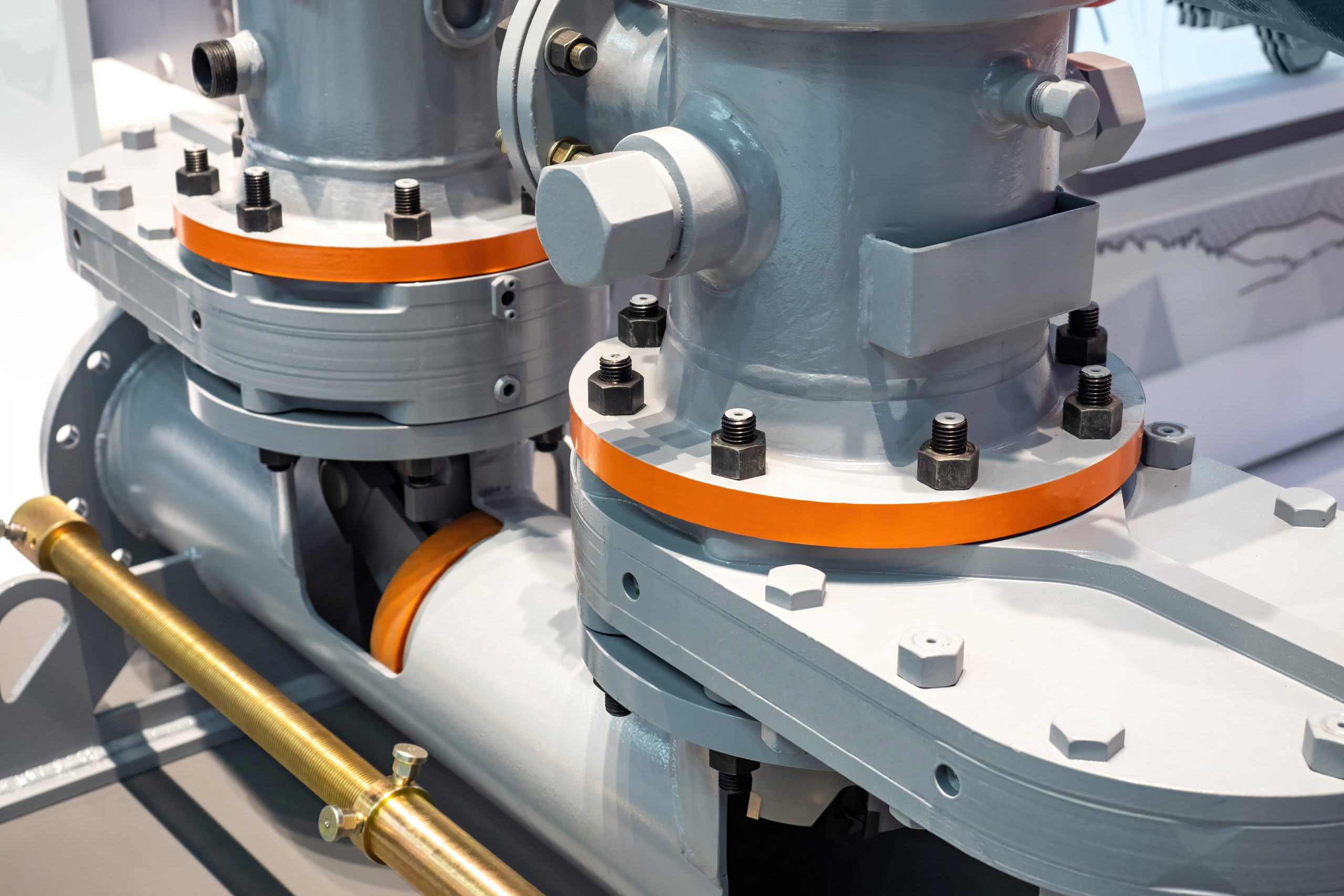
Whether in the energy, mining or machinery industries, our spacers enable miniaturization and reduce energy consumption by increasing the coefficient of friction.
Wind and water power
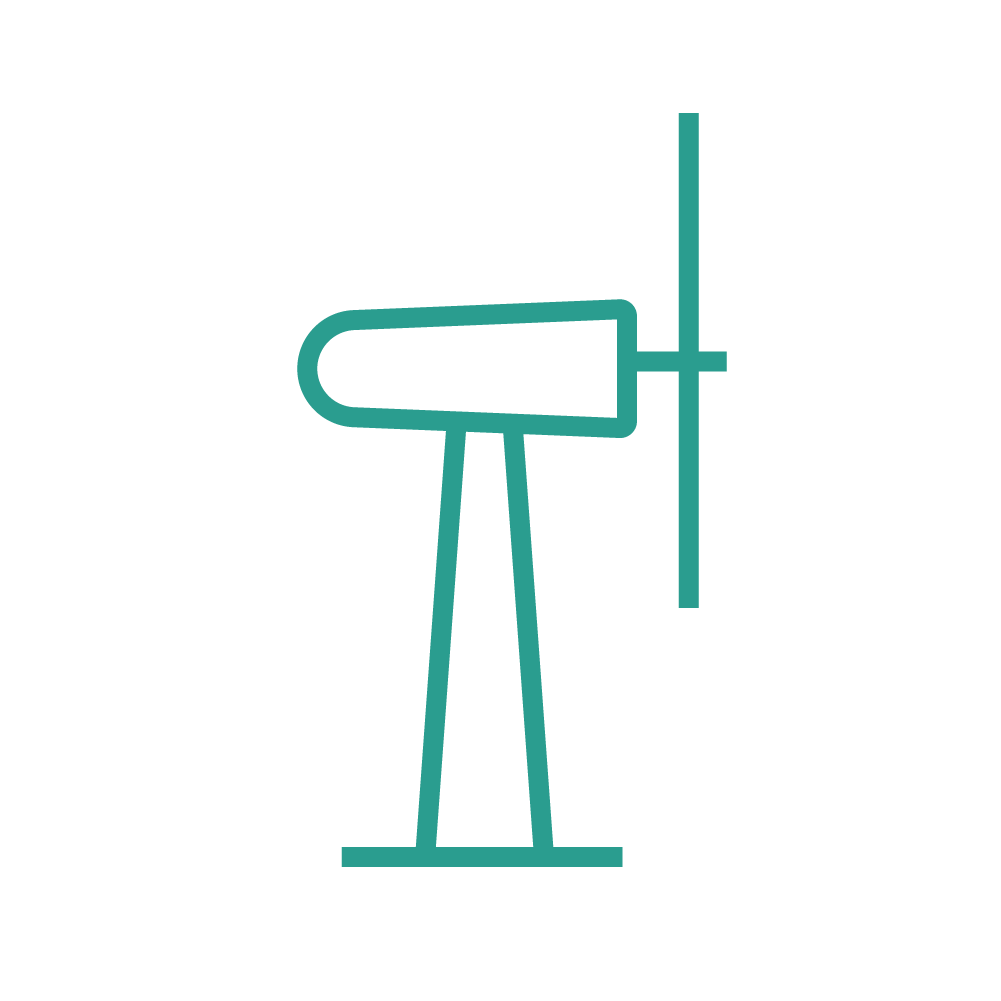
In general, to transmit higher torques in flanges or drive shafts, the components or fastening system must be enlarged or multiplied. This will have an impact on size and weight, while increasing the cost of the system as a whole.
How does it work?
A better approach is to use DIANIP friction spacers to reduce the weight and size of the connections between the shaft and the rotor hub of a wind turbine. Reducing the size of these assemblies increases maximum torque transmission, reduces the number of bolts in flange connections, and thus achieves better performance with a smaller assembly. The aim is to increase the coefficient of friction between components instead of increasing component size.

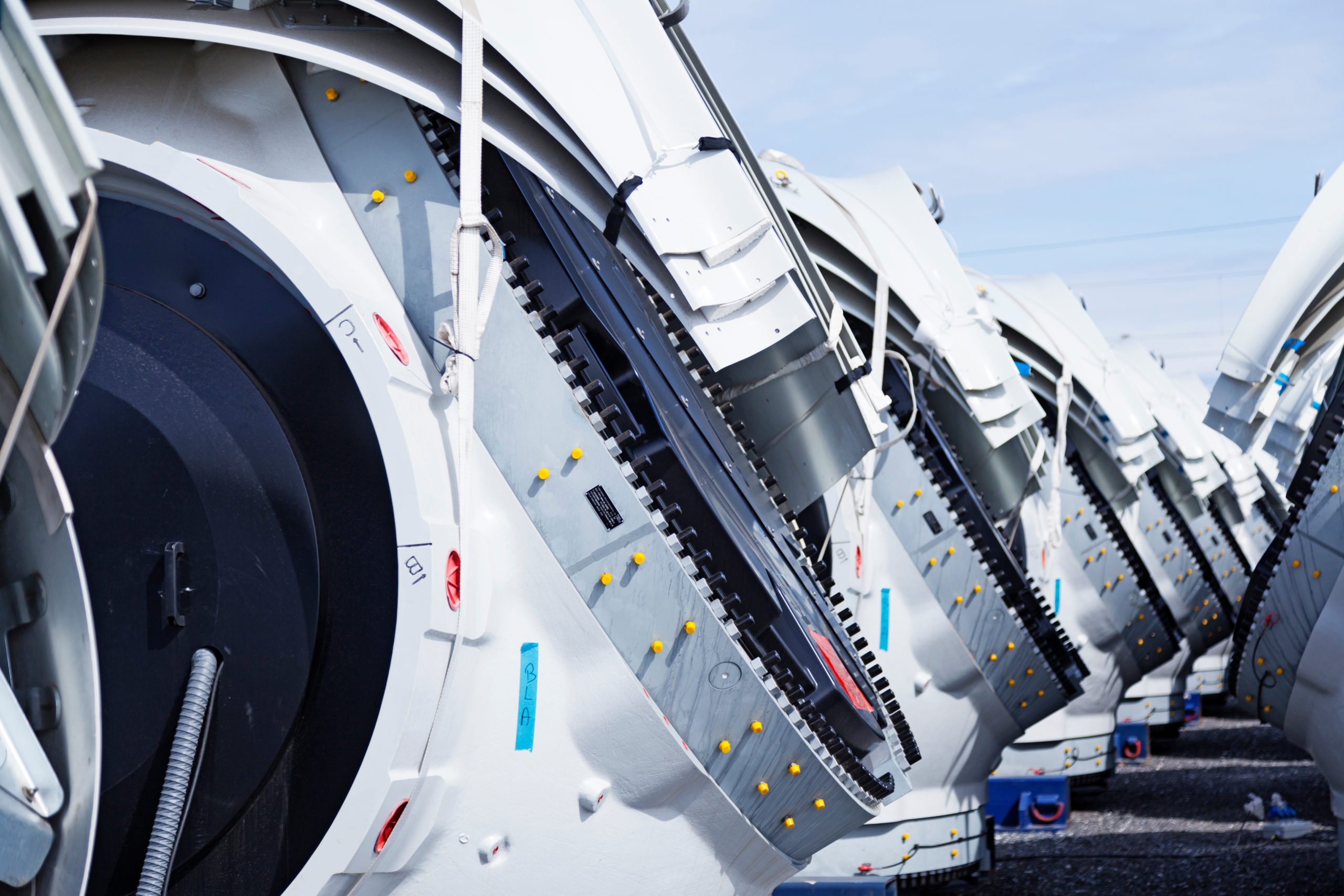
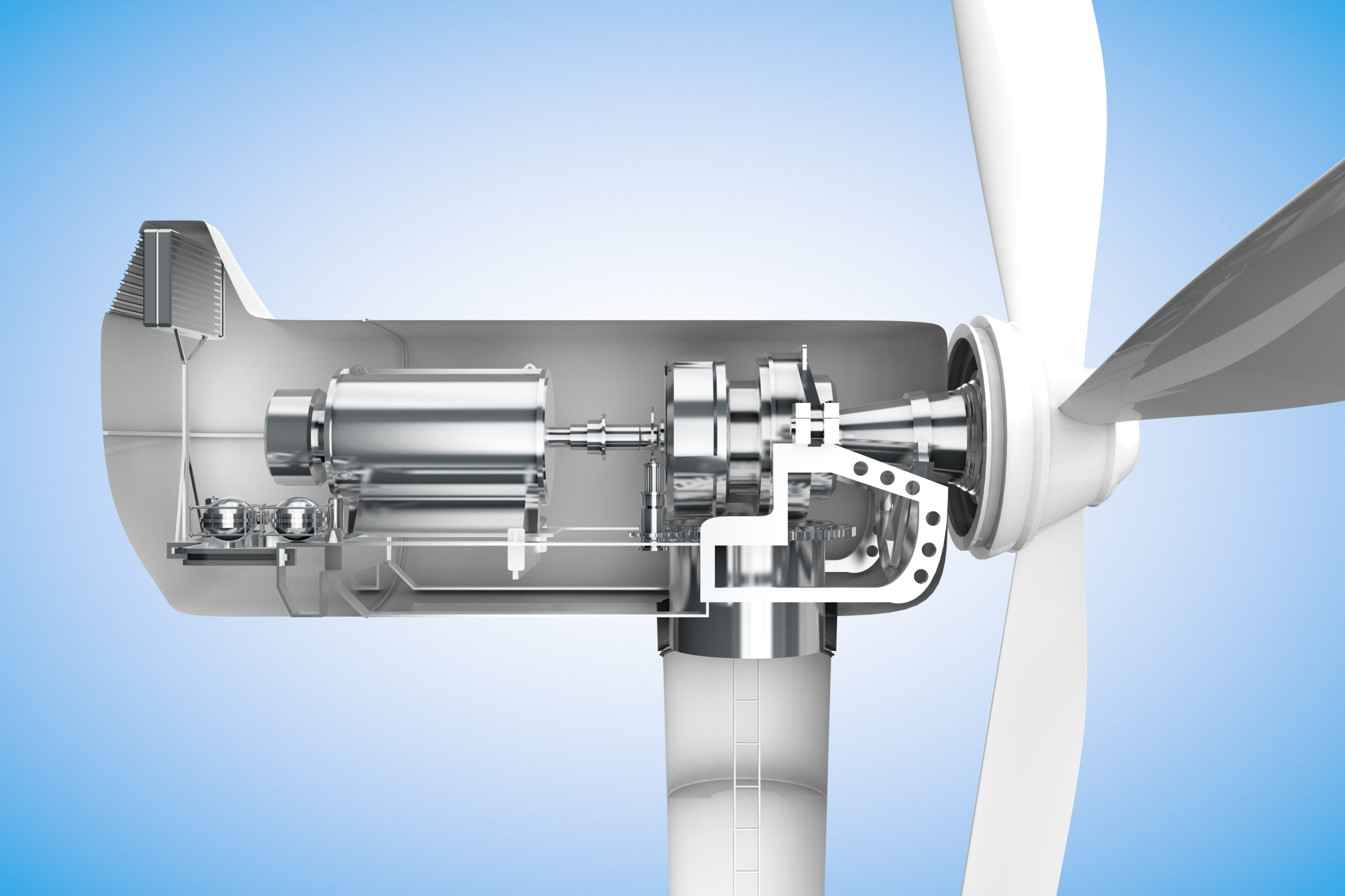
DIANIP Friction Shims are used in various applications within a wind turbine, such as: flange connections between the main shaft and the gearbox, flange connection between the rotor blades and the hub, connection between the pitch motor and the hub, and inside the gearbox.
Benefits
Increasing the functionality of mechanical parts optimizes critical properties and offers the following benefits:
Higher torque transmission
No system changes
Reduced assembly size and weight
Increase safety margin
Noise reduction
Easy to assemble and replace
Properties
Information | Dianip G10 | Dianip G13 | Dianip G25 | Dianip G35 | Dianip G50 |
---|---|---|---|---|---|
Average particle size | 10 μm | 13 μm | 25 μm | 35 μm | 50 μm |
Hardness of NiP matrix | 400-600 HV 0.1 | 400-600 HV 0.1 | 400-600 HV 0.1 | 400-600 HV 0.1 | 400-600 HV 0.1 |
Thickness of NiP matrix | 6-10 μm | 8-12 μm | 15-19 μm | 19-27 μm | 28-36 μm |
Total coating thickness | 15 μm ± 10 μm | 17.5 μm ± 10 μm | 30 μm ± 10 μm | 45 μm ± 15 μm | 65 μm ± 25 μm |
Total thickness (raw spacer 100μm) | 130 μm ± 20 μm | 135 μm ± 20 μm | 160 μm ± 20 μm | 190 μm ± 30 μm | 230 μm ± 50 μm |
common features
Form | According to customer request |
Colour | Silver-grey metallic |
Substrate | Spring steel |
Spacer thickness | Laser cut/stamped |
Die material | Nickel-phosphorus alloy |